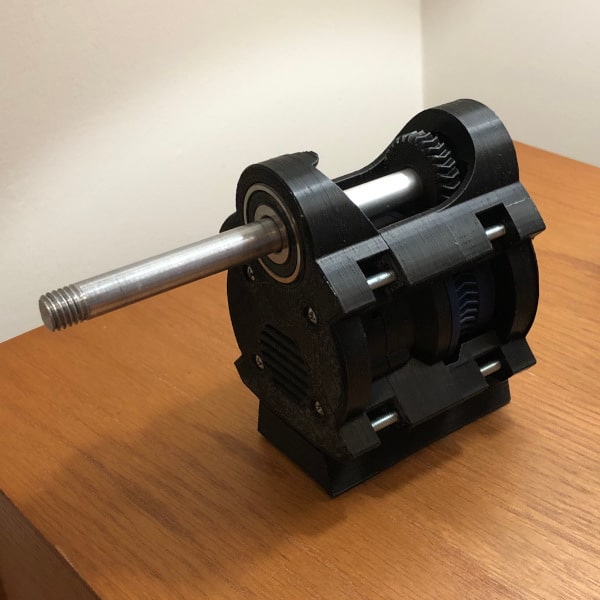
So I may have gotten a little ahead of my skis with the next-gen star tracker. I like the design and the look but the problem is that it just doesn’t work. Niedobrze… That’s the bad news. The good news is that I think that I managed to get to the bottom of the problem. Spoiler alert, non-meshing gears weren’t the only problems that I had. So while the first and second iterations of my next-gen star tracker design have ended in failure, I’m not about to give up on this concept. And hey, at worst I’ve still got the Gamma star tracker to fall back on.
I Should Have Known
Well, in fact, I kind of did. I knew I was really pushing the limits of my 3D printer with the gear sizes. But I thought I would be able to design around this limitation. I ended up designing a top carrier arm to hold the gears firmly in position. And this actually worked quite nicely. Unfortunately, though, this was not enough to overcome the lack of gear tooth precision that I was attempting to achieve with a module of 0.6. Of course, I did this to shrink the overall footprint of the design. But when trying to print features that were a smidgen smaller than my nozzle diameter of 0.4mm the wheels fell off the bus. I’ll spare you the fuzzy photos and analysis that I gathered from testing this – but it was … bad.
I was asking for trouble and I knew it. Even after fixing that whole debacle with the maths brain cramp which resulted in a non-meshing gear stage. The bottom line is that this star tracker design is a proper failure. So it’s time to start an iterative revision process.
Back to Basics
I’ve been pushing the boundaries of what is possible with this project. I think this was a noble goal. But at the end of the day, I want something that works and works reliably. Size isn’t the be-all and end-all of this design. Yeah, it would have been super sexy to have a pocket-sized tracker. But what’s the point if it isn’t functional? So what went wrong?
Well, I designed the internal gears with a module of 0.6 and a pressure angle of 14.5 degrees. Maybe I could have gotten away with this on a resin printer, but not my Adventurer 3 FDM printer with a 0.4mm nozzle. Yeah, I know, I know. But can you seriously blame me for trying? Actually, I’m claiming victory based on the fact that it worked at all. But it just didn’t work reliably. So I’ve made a couple of revisions to the design to hopefully get things back on track.
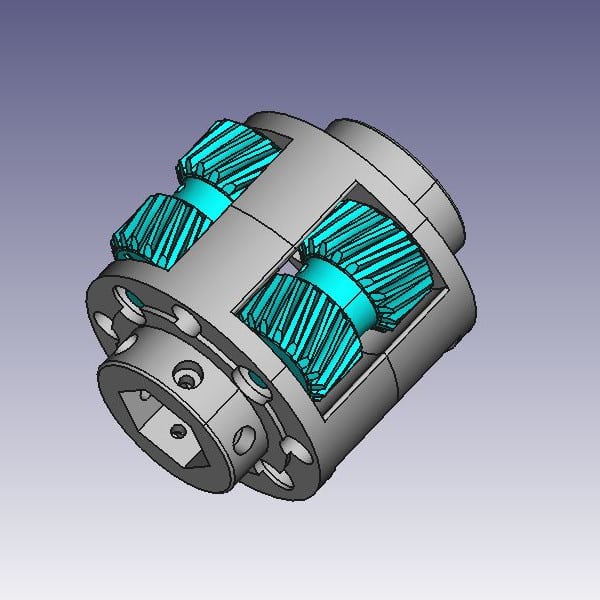
One is a nice number. So revision one is to bump the base module for this design up to 1. Yeah, it’s like twice the size, but I’ll get much more reliable gear dimensions. For revision two, I’m going to cage-mount all the planet gears. I kinda didn’t want to do this, but I think this is the best way to keep everything balanced and aligned in the split-ring planetary gearbox. The result is just a little bulkier. So I designed and printed a new test rig with these modifications. Hopefully, this will elevate my star tracker design rating from failure to the pinnacle of awesomeness. Well, I can dream, can’t I?
Awesomeness May Have to Wait
So I have my revised and beefy Snorlax design ready to go. OK, I know this print is a bit loud. I’m just testing my revisions at this point…
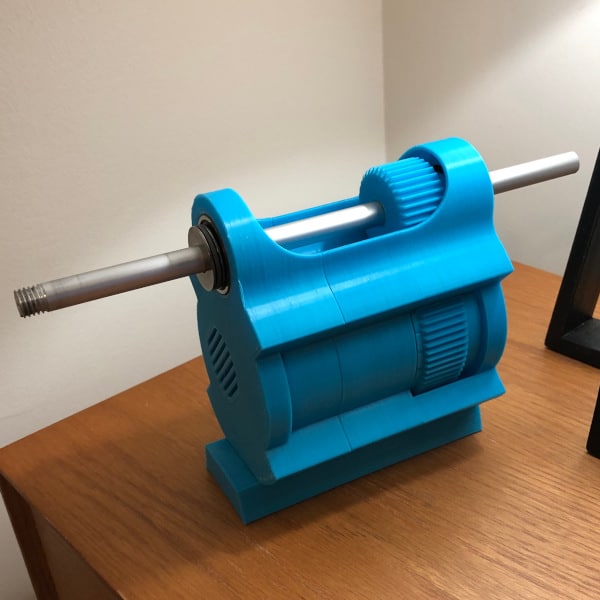
Some very pleasant weather yesterday was a welcome sight. So I got out and ran some 30-second exposure tests. Let me just skip to the punchline and say that these revisions resulted in much better star tracker performance. However, they’re still not as good as they need to be if I’m going to switch over from Gamma. Here’s a breakdown of the image quality of the test run.
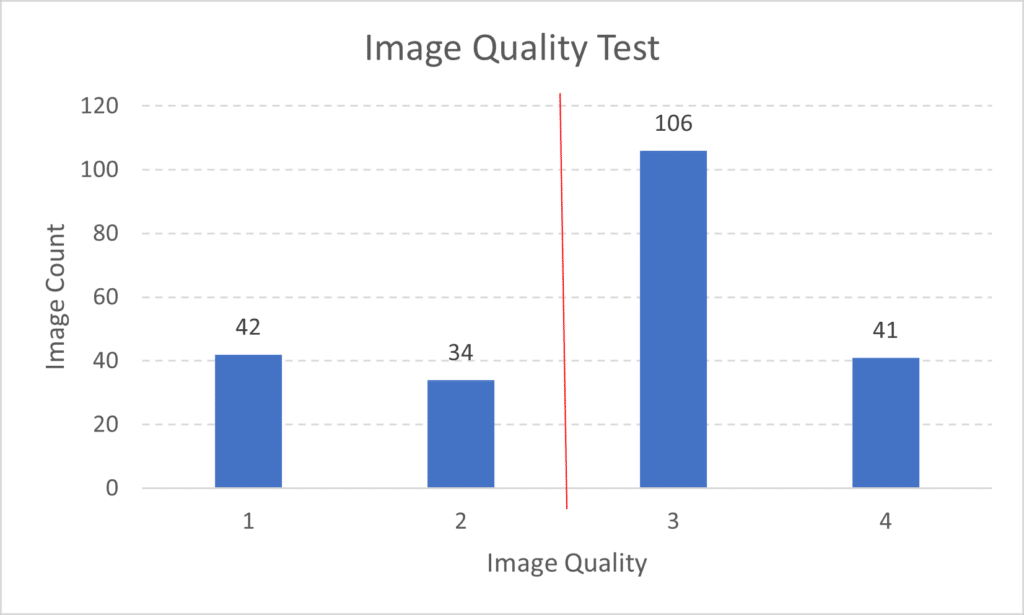
I can appreciate that image quality can be a somewhat subjective measurement. So here is a representative sample of my image quality ratings.
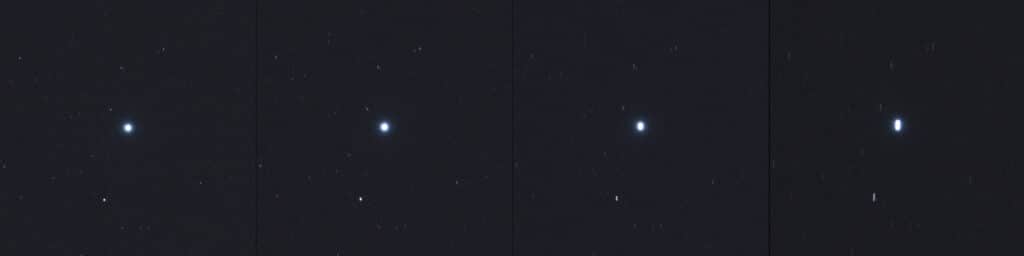
Image quality 1 is what I would subjectively call perfect and 2 would be an image with less than a half-star width of star trail. I’m comfortable stacking both of these kinds of images. Image quality 3 is an image with major star trails or dumbbell stars. Quality 4 is just rubbish. So as you can infer, only getting 33% of photos that are stackable is quite poor. When it comes to the star tracker design, it’s still solidly rated as a failure.
New Problems Require New Solutions
I really feel like I’m close. After inspecting my session photos, it appears that the image wonkiness is still being caused by the meshing gears. I say this because of the dotted-line type star trail pattern that dominates my photos. And that got me thinking…
I’m using helical gears on the split-ring planetary gearbox. Due to the nature of FDM printing, I’m always going to be living with printed layers slipping over other printed layers. And when you have helical gears meshing (or worm gears for that matter), they’re not sliding over a smooth surface. It’s more like two staircases sliding over each other. Once again, maybe with a different printing technique, this wouldn’t be a problem. But I’m confident that the image distortions that I’m seeing are happening on an extremely small scale in my device – fractions of millimeters.
If my input was a high RPM motor, I doubt you’d even notice these very very very very small errors. My problem is that I’m trying to control my tracker to rotate at defined intervals by fractions of a degree. And I’m expecting the tracker to perfectly execute these movements. Yep, it’s a tall order for sure.
So I think for my next revision, I’m going to do two specific things. First, I’m going to switch back to an involute gear profile. I’m not overly concerned about noise given the nature of my design and the speeds I’m working with. But I think that the flat-facing surfaces will mesh together better. Second, I’m going to attempt to “burn-in” my gears. In other words, I’m going to assemble the gearbox and then run it unlubricated with a higher RMP motor for a period of time. Hopefully, this will wear down any burs or anomalies in the gears.
Moving Forward
So, now you know what I’m working on. I’ll need several days to print the latest revisions and then some clear skies to see if these changes make a difference. I’d be ready to walk away if I didn’t think I was close. And, I have a couple of other thoughts on how I might tweak things further. But, I’m still having fun messing around with this project. And of course, I’m really looking forward to taking this star tracker design failure and turning it into a winner!